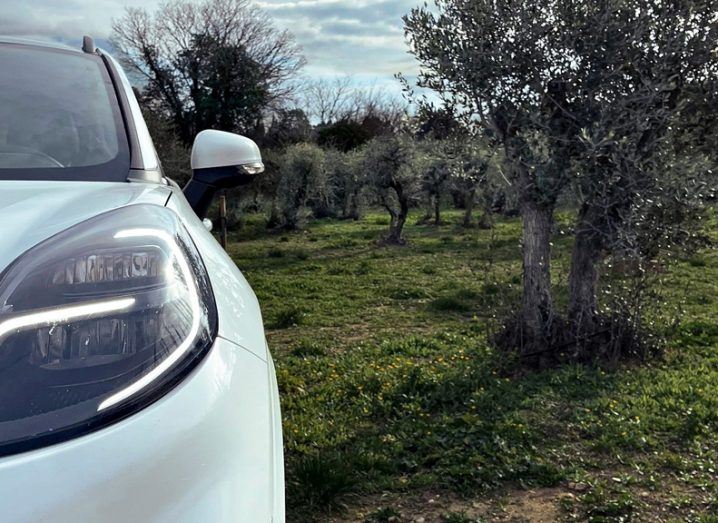
Image: Ford
Using olive tree waste from Andalusia, Spain for auto parts could reduce the use of plastic and support cleaner air in the areas the trees are grown.
US car manufacturer Ford is exploring the use of discarded parts of the olive tree to make auto parts in a push for greater sustainability in the industry.
The company with EU headquarters in Cologne, Germany is using olive branches, twigs and leaves that are disposed of during the harvest months as part of a trial that seeks to reduce the use of plastic and and create more sustainable parts for mass use.
Ford believes using olive tree waste for auto parts, a project it calls COMPOlive, could support cleaner air in the areas the trees are grown by preventing the burning of waste as is the standard practice during harvest.
Parts made from the olive tree branches, twigs and leaves include footrests and parts of the boot area of cars. Ford engineers testing the materials have found that the parts are both “robust” and “durable”, potentially paving the way for mass use in electric cars.
“At Ford, we’re always looking for ways to become more sustainable and sometimes inspiration can strike from the most unlikely places,” said project lead Inga Wehmeyer.
“In using the waste from olive trees, we have been able to substitute a significant amount of petroleum-based raw material in the interior parts. The sustainable fibres create a unique surface appearance and would be directly visible to our customers.”
As part of the COMPOlive trial, waste materials were sourced from olive groves in the Andalusia region of Spain, known for being one of the biggest producers of olive oil in the world.
Ford said engineers at its European headquarters in Cologne used simulation technology to test the usability of olive trees in terms of durability, strength and mouldability before manufacturing the prototypes.
Made of 40pc fibres and 60pc recycled polypropylene plastic, Ford said the substance was heated and injection moulded into the shape of the selected part.
“In order to get the mix just right, we had to experiment with different ratios of waste material and polypropylene,” said injection moulding expert Thomas Baranowski. “It was hard work, but it ultimately enabled us to produce a material that shows no compromise in strength, durability or flexibility.”
10 things you need to know direct to your inbox every weekday. Sign up for the Daily Brief, Silicon Republic’s digest of essential sci-tech news.