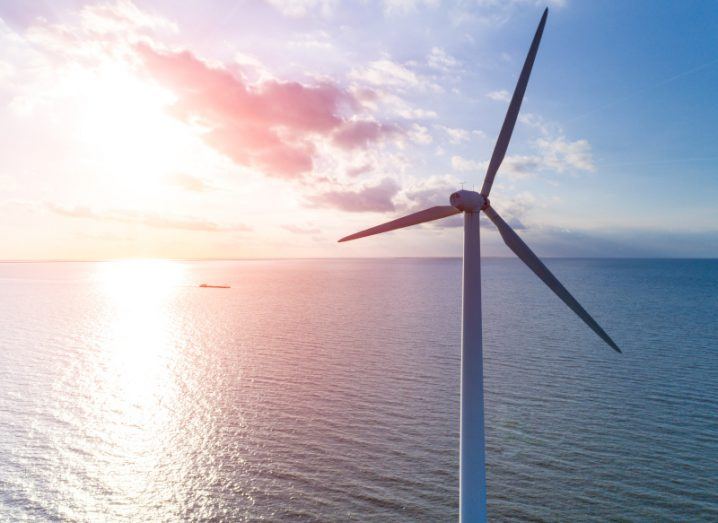
Image: © Stockr/Stock.adobe.com
University of Oxford’s Dr Emma Edwards describes the latest innovations in offshore wind turbine platform design.

A version of this article was originally published by The Conversation (CC BY-ND 4.0)
Yes, you read that right – float. You may have seen a wind turbine in the sea before, but chances are you were looking at a ‘fixed’ turbine – that is, one that sits on top of a foundation drilled into the seabed. For the new frontier of offshore wind power, the focus is on floating wind turbines. In this case, the turbines are supported by floating structures that bob and sway in response to waves and wind and are moored with chains and anchored to the seafloor.
This is becoming the focus of the sector for the simple reason that most wind blows above deep water, where building fixed platforms would be too expensive or simply impossible. Designing these new floating platforms is a true engineering challenge, and is a focus of my academic research.
These wind turbines are enormous, reaching up to 240m tall – about the size of a skyscraper. Since they are so tall, strong winds far above the sea surface tend to make the turbine want to tilt, so platform designs focus on minimising this tilt while still being cost-competitive with other forms of energy.
There are more than 100 ideas for platform designs, but we can broadly group them into the following six categories.
Spar
Spars are narrow, deep platforms with weight added to the bottom to counteract the wind force (this is called ‘ballast’). They are usually relatively easy to make because they normally consist of just one cylinder.
However, they can extend 100m or more underwater, which means they can’t be deployed in normal docks which are not deep enough. Specialist installation procedures are required to install the turbine once the platform has been towed into deep water.
Barge
Barges are wide, shallow platforms that use buoyancy far from the centre of the structure to counteract the wind force on the tower. As they usually extend less than 10m underwater, they do not need any specialist deep-water docks or installation vessels.
However, they can be difficult to make because the platform is usually a single, large unit with a complex shape.
Tension-leg platform
Tension-leg platforms (TLPs) use taut mooring lines to connect the platform to the seabed and stop the turbine from tilting in the wind.
These platforms are usually smaller and lighter than the other types, which makes them easier to fit at a standard port. Also, their seabed ‘footprint’ is small due to the taut lines.
However, the platforms are usually not stable until attached to their mooring lines, meaning that a special towing and installation solution is required.
Semi-submersible
Semi-submersibles consist of three, four or five connected vertical cylinders, with the turbine in the middle or above one of the columns. The platform utilises buoyancy far from the centre (similar to the barge) and ballast at the base of each column (similar to the spar).
Like barges, semi-submersibles do not require specialist tow-out equipment and work for a wide range of water depths. Manufacturing is again a challenge.
Combination-type
The four categories above are the more ‘traditional’ platforms, influenced by their predecessors in the oil and gas industry. Since the 1960s, floating platforms have meant huge oil rigs can access deeper water sites (the deepest is over 2,000m). Most of these oil rigs in deep water are either semi-submersibles, anchored to the seabed with chains, or TLPs, connected to the seabed with taut cables.
More recently, there has been a trend towards platforms more specialised to floating wind. Specifically, some use a combination of the stability mechanisms, taking advantages from each of the previous designs.
For example, ‘lowerable ballast’ platforms look like traditional semi-submersible or barge platforms, but with a weight hanging from taut cables.
During turbine installation at the port and tow-out, the weight is raised, so that a traditional (non-deep) dock can be used and no specialist equipment is needed. At the site of installation, the weight is lowered and the platform gets extra stability from a low centre of mass.
Other designs use the benefits of stability from taut mooring lines (similar to a TLP) but are designed to be stable during tow-out and so don’t need a special installation vessel.
The taut mooring lines are attached to a single column, which is installed initially. The rest of the platform, which is self-stable, is then towed out and connected to the pre-installed column with the taut mooring lines. The platform uses the extra stability from the mooring lines but without the tow-out instability typical of TLPs.
Hybrid platforms
These platforms add another type of renewable energy, most commonly a wave energy converter. This increases the overall amount of energy generated, and reduces costs as power cables, maintenance and other infrastructure can be shared.
A wave energy converter also reduces platform motion, which in turn increases the power performance from the turbine.
Room for improvement
Four floating offshore wind farms have already been built, the largest of which was opened in 2023 off the coast of Norway. Two of these farms use the Hywind spar design and two use the WindFloat semi-submersible.
There have been 18 other platform designs to reach at-sea testing, including at least one of each of the categories described above. Some have plans to build floating farms in the next few years, and additional early-stage designs have plans to deploy their own prototype devices in the near future.
Interestingly, platforms are actually diverging in design. After many years, wind turbines have mostly converged on the three-bladed design that you see today, but there has been no such convergence yet on a consensus ‘best’ floating platform. This suggests significant improvements are still possible, especially in terms of reducing motion and decreasing cost.
Dr Emma Edwards is career development fellow in engineering at St Peter’s College, University of Oxford. She completed a PhD at MIT in 2020. Her research focuses on fluid mechanics and its application to offshore renewable energy.
Find out how emerging tech trends are transforming tomorrow with our new podcast, Future Human: The Series. Listen now on Spotify, on Apple or wherever you get your podcasts.