
Image: Eli Gershenfeld/NASA Ames Research Center
A new wing made from hundreds of tiny components designed by NASA and MIT promises a paradigm shift in efficiency compared with older designs.
In the near future, aircraft could look substantially different from what we are used to today, particularly when it comes to the shape of their wings. One such new design has been revealed by MIT, in conjunction with NASA, and it could allow for a wing to change shape mid-flight, making manufacturing much easier and flight far more efficient.
The new design, published to Smart Materials and Structures, does away with separate movable surfaces such as ailerons to control the roll and pitch of the plane. Instead, the wing is assembled from hundreds of tiny identical pieces that make it possible to deform the entire wing, or just part of it, by incorporating a mix of stiff and flexible components in its structure.
These tiny components are bolted together to form a lightweight lattice, which is then covered with a thin layer of polymer material. The resulting wing is significantly lighter than conventional designs, making it much more energy-efficient than even the most modern wings made from composite materials.
While standard wing design tries to incorporate the different phases of flight – such as take-off, cruising and landing – the rigid structure only results in a compromise that isn’t very efficient. So, a wing that is constantly deformable would be a significant boost to air travel.
The researchers also took the new wing a step further by designing a system that automatically responds to changes in its aerodynamic loading conditions, by shifting its shape without the need for additional motors or cables.
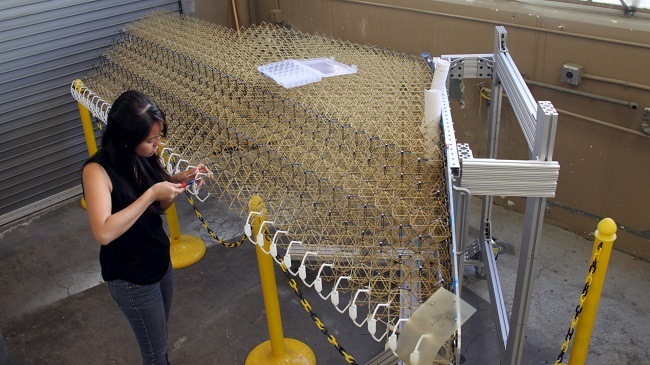
Image: Kenny Cheung/NASA Ames Research Center
Assembled by robot swarms
“We’re able to gain efficiency by matching the shape to the loads at different angles of attack,” said Nicholas Cramer, the paper’s lead author. “We’re able to produce the exact same behaviour you would do actively, but we did it passively.”
Unlike the prototype that was built by hand, the real wing could be easily assembled by a swarm of small, simple, autonomous assembly robots. Using a waterjet cutter and 3D printer, each part could be produced in as little as 17 seconds, making the process ideal for mass production.
The resulting lattice produced by the method had a density of 5.6kg per cubic metre, compared with rubber, which has a density of 1,500kg per cubic metre. Also, the fact it is made from tiny subunits means the wing can be made into any shape as desired.
The concept is not just limited to wing design, the researchers said, as it could also be used for wind turbine blades, where the ability to do on-site assembly could avoid the problems of transporting ever-longer blades. It could even be used to build space structures, as well as bridges and other high-performance structures.