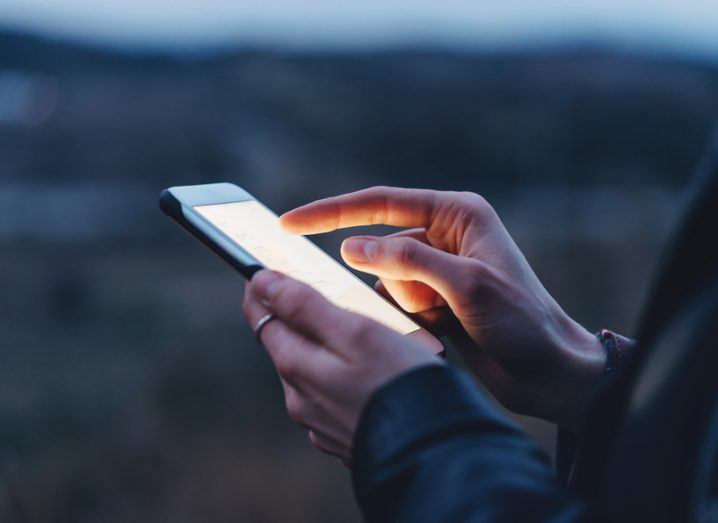
Image: FlyingFifeStudio/Shutterstock
The AMBER centre has been set the task of creating scratch-free surfaces to overhaul the optics and auto industries as part of an €8.2m EU fund.
Trinity College Dublin’s (TCD) AMBER centre has done pretty well for itself over the years, and is now set to receive new funding to pilot the mass production of anti-reflective, scratch- and abrasion-resistant surfaces that can be applied on camera lenses, car components and mobile phones.
Current anti-reflection solutions typically rely on thin-film coatings comprising multiple layers of materials deposited onto each and every reflecting surface along the optical path.
Production methods for this technology in its current state are not commercially viable as they are energy-intensive and highly precise.
Called Sun-Pilot, the €8.2m project will span four years, raised mostly from the EU Horizon 2020 (H2020) programme, with an additional €1.1m coming from industry.
Its focus will be developing new technologies for the optics and automotive industries, where strong surfaces are expected to have the greatest impact.
Largest TCD funding to date
Led by AMBER’s senior research fellow, Dr Parvaneh Mokarian, the project will involve 13 partners from six European countries, with AMBER receiving €2.1m of the total sum.
This makes it the largest amount TCD has received as part of a collaborative H2020 project.
“Sun-Pilot will look to reduce the cost of anti-reflective precision optics manufacture by at least 75pc by replacing complex and demanding anti-reflective multilayer coatings with a single nano-patterned surface,” Mokarian said.
“We are confident that our research will have a major impact for both the optics industry and in the automotive industry.”
Cheap to make
Sun-Pilot will develop the new anti-reflection and scratch-resistant technologies using the Zeroptica surface nano-patterning process developed and patented by Mokarian in AMBER, which can be applied across a range of materials.
The technology is based on structured molecular units called block copolymers, which can deliver self-assembled nano-patterned masks onto any curved surface or other large areas such as solar cells.
“It is also cheap and doesn’t require any expensive equipment,” Mokarian added.
“Other available techniques used today either use harsh chemicals for patterning, which are not environmentally friendly or require expensive equipment or can only be applied on flat surfaces.”
Its uses within the auto industry could involve developing nano-patterning moulds for injection moulding of plastic parts to achieve functionality such as soft touch or enhanced colour.