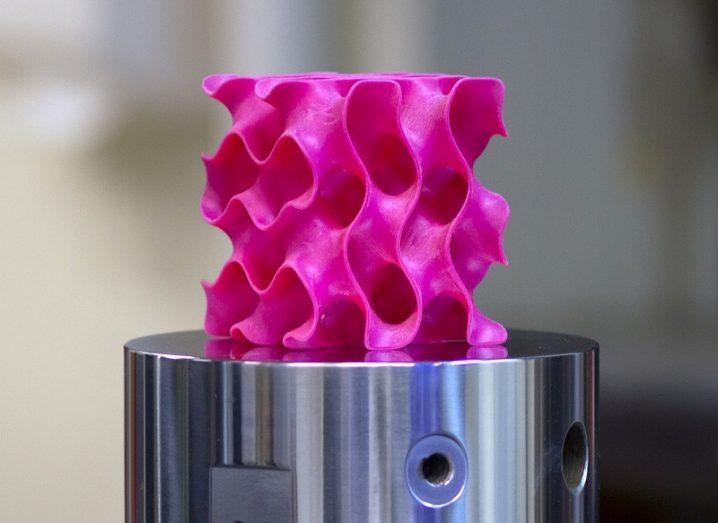
The 3D printed material made using graphene. Image: Melanie Gonick/MIT
The potential benefits of graphene are about to go 3D, as an MIT team has revealed a new material that is the lightest and strongest known to date.
Previous breakthroughs in the field of graphene have demonstrated enormous potential for graphite material just one atom thick, but the latest development has shown that it can also be incredibly useful in 3D applications.
According to MIT News, a team from the prestigious university has found that by compressing and fusing flakes of graphene, they were able to build a 3D-printed material that is 10 times stronger than steel, but 95pc lighter.
Resembles natural coral
Resembling a porous Nerf ball – known as a gyroid – the compressed graphene is incredibly complex, to the point that trying to replicate it using conventional manufacturing might be impossible.
Publishing its findings in the journal Science Advances, the team led by Markus Buehler was able to surpass previous failures by analysing graphene down to the atomic level to see why the material has been difficult to use in 3D.
By compressing small flakes of graphene with heat, the material was able to transform into a strong and stable structure that closely resembled natural corals and microscopic creatures.
The strength of the material comes from its shape, as its large surface area in proportion to its volume proves to be a mathematically ideal ratio.
Not just for use with graphene
Drawing a comparison with a readily available material, Buehler has said that while a sheet of paper is easily foldable and weak, sheets of paper rolled into a tube will significantly strengthen along its length.
This same principal allows the geometric arrangement of graphene flakes to become incredibly strong.
Interestingly, the team has said that despite using graphene because of its durability, the strength in the material lies in the structure’s geometry.
“You can replace the material itself with anything,” Buehler says. “The geometry is the dominant factor. It’s something that has the potential to transfer to many things.”
The geometric model, he continued, could be applied on a much larger scale, such as use in structural materials, and its microscopic porous nature could also allow for use in filtration systems.